Introduction
Les normes qualité ISO indiquent en dernier point la nécessaire utilisation des statistiques. Ce qui n'est pas précisé c'est comment faire. Ceci conduit à la mise en place des outils décrits par ailleurs. Les plans d'expériences pour l'amélioration d'un procédé. Les cartes de contrôle et indices de capabilité pour le suivi. Par contre l'intégration de ces outils est plus difficile à mettre en oeuvre. Une des questions de la qualité est la relation avec un nouveau client ou une nouvelle pièce. Comment en déterminer notre capabilité à la produire ? Plus généralement comment faire le lien entre les outils des statistiques de la qualité et les outils du bureau des méthodes ?
Nous allons donc voir en premier les méthodes actuelles et leurs limites.
Puis une nouvelle simulation d'usinage en lien avec la démarche qualité :
Les liens actuels entre le Bureau d'études (BE) et l'atelier.
Le cheminement d'un projet part d'une demande client jusqu'au bureau d'études. Celui-ci va réaliser des plans d'ensemble des pièces à réaliser. Ces plans font apparaître les contraintes à respecter. En général des dimensions, des jeux des états de surface.
Ceci se répercute sur chaque pièce sous forme de dessin de définition avec les conditions à respecter : cotes, position (perpendicularité, coaxialité...) état de surface...
l'établissement d'un processus d'usinage à partir de ce dessin se fait suivant une méthode d'analyse connue (NF E-550 / 551 /552 / 553)
Elle se décompose en les étapes suivantes.
Analyse des contraintes :
- contraintes de cotation
- contraintes de spécification
- contraintes technologiques
Définition des opérations :
- opérations élémentaires
- groupements de surfaces
- contraintes d'antériorité.
Le tableau ou le graphe des antériorités va être récapitulé dans une matrice des antériorités. Celle-ci élevée à la puissance n doit donner 0. Une autre valeur signifie une incompatibilité. Cette méthode matricielle est utile pour trouver les incompatibilités d'ordre supérieur à 2. Ceci se manifeste par une boucle sur le graphe.
Pour un usinage on va devoir choisir une étape de départ. Pour cela on doit monter la pièce brute sur la machine en utilisant un référentiel de départ. Le critère K=surface/intervalle de tolérance est choisi. Surface : nombre de normales à la surface du brut ; IT : plus petit intervalle de tolérance pour une cote de liaison à cette surface brute.
Dans l'analyse isostatique on va mettre le maximum de normales sur les surfaces où K est grand. Total maxi de normales 6. Surface = nombre de normales maximum :
- plan 3
- cylindre 4
- cylindre court 2
- ligne (surface en forme linéaire) 2
- point (petite surface) 1
En continuant la description des étapes on va obtenir un avant projet d'usinage. Cet avant projet fait apparaître des cotes de fabrication. Ces cotes représentent aujourd'hui dans l'atelier la qualité demandée par le client. Nous allons voir deux méthodes de calcul de ces cotes. Elles seront détaillées dans un exemple. Puis, dans la discussion nous analyserons les atouts et les points faibles de ces modes de calcul.
La première vignette reprend le dessin BE avec les cotes à atteindre. Puis on a le dessin du Brut avec les cotes associées. Dans la phase 10 on remarque en vert l'isostatisme avec le 3 encadré représentant un appui plan et en rouge la surface usinée. En phase 20 n'est dessinée que la pièce terminée mais une phase d'ébauche est nécessaire avec une cote machine cm2'. En phase 30 la cote machine est entre le bord de la pièce et le centre du trou. Le diamètre du trou est une cote outil.
Pour faire une simulation d'usinage, le dessin est déformé jusqu'à devenir difficilement reconnaissable de telle manière à faire apparaître toutes les surfaces. Pour se repérer on numérote ces surfaces. Ici 5 représente la surface finie, 6 l'ébauche et 7 le brut.
Dans les deux dernières simulations apparaissent 4' et 5' qui correspondent à la variation due au positionnement de la pièce dans le porte pièce.
Pour pouvoir suivre les calculs vous pouvez imprimer l'image ci dessus (clic droit puis imprimer l'image). Vous pouvez aussi enregistrer la page sur votre disque et l'imprimer en entier.
Calcul des cotes de fabrication (CF) méthode classique.
Quand la cote d'usinage ne correspond pas à une cote du bureau d'études (BE) elle est obtenue par le calcul. On calcule les cotes de fabrication en fonction des cotes bureau d'études par calcul vectoriel. L'intervalle de Tolérance (IT) de la cote BE est égal à la somme des IT des cotes d'usinage. Ceci donne par exemple condition minimum = somme des cotes d'usinage au minimum pour celles qui sont dans le même sens que le vecteur BE moins somme des cotes d'usinage maximum pour celles qui sont en sens contraire au vecteur BE.
- Avantages de cette méthode
- Elle est connue et facile à mettre en oeuvre puisqu'il s'agit de la résolution d'équations à une inconnue.
- Inconvénients de cette méthode
- La simulation classique ne tient pas compte des variations dues à la mise en place de la pièce sur le porte pièce.
- Elle n'est pas directe car on peut tomber sur des impossibilités dues au fait que les premières cotes calculées sont un IT important ce qui pèse sur les suivantes.
Par exemple : soit une cote BE d'IT 0,6 elle est obtenue avec les cotes transférées U1 et U2.U1 et U2 vont avoir comme IT 0,3.Soit une seconde cote BE d'IT 0,4 elle est obtenue avec les cotes transférées U1 et U3.U1 a déjà comme IT 0,3 il ne reste que 0,1 pour U3.Ces calculs ne tiennent absolument pas compte de la capabilité de la machine. Ainsi l'IT est réparti uniformément alors que dans la chaîne de cotes certaines étapes sont manifestement plus précises que d'autres.
- D'autre part, on calcule en tenant compte des cas les plus défavorables en plus ou en moins. Dans une chaîne de cotes de 3 vecteurs si le cas défavorable pour une cote est une fois sur100, alors le cas défavorable pour la chaîne est une fois sur1.000.000. Statistiquement cette méthode de simulation peut être améliorée.
- D'autre part avec ce système on est obligé de faire des hypothèses qui peuvent être contraignantes en effet quand on choisit 2 comme écart sur le brut on lui attribue un écart type de 0,33 ce qui peut être optimiste.
Méthode utilisant une répartition par poids
Cette méthode est utilisée pour améliorer la répartition des IT en tenant compte des modes de fabrication. Chaque cote condition BE ou BM est représentée en tant que cote bilimite centrée sur son IT. De cette manière la valeur centrale de chaque cote de fabrication se calcule immédiatement par addition ou soustraction. Chaque étape est liée à son mode de réalisation, de celui-ci on connaît la précision. Par exemple on sait que la précision d'une ébauche est moins bonne que pour une finition. L'IT à répartir se fait donc en utilisant une clef liée à son mode de réalisation. Par exemple dans une chaîne de cotes il y a un IT de 0,3 à répartir. Si, dans la chaîne il y a une CF d'ébauche et une CF de finition le coefficient de l'ébauche étant plus fort que celui de la finition l'IT pourra se répartir comme suit : 0,2 pour l'ébauche ; 0,1 pour la finition. L'ordre des calculs ne se fait plus en recherchant en premier les équations à une variable mais en utilisant un critère lié à la précision BE et aux coefficients. Il n'y a donc plus de cas d'IT inférieur à zéro. Critère utilisé : IT restant à répartir / somme des poids restant des CF non calculées de la chaîne de cote.
- Avantages
- cette simulation tient compte des variations dues à la mise en place de la pièce sur le porte pièce.
- simplicité du calcul des CF nominales.
- On tient compte de la façon de réaliser la cote pour attribuer l'IT.
- Plus de cas d'IT inférieur à zéro.
- Inconvénients
- Calcul des IT un peu plus compliqué que précédemment.
- Ne donne toujours pas d'indication sur la capabilité à produire.
- Difficulté de choix des poids.
Une troisième voie : l'utilisation des statistiques de la qualité
Le cadre de travail.
On va supposer que l'on connaît les caractéristiques de notre outil de production. Ici la précision représentée par les écart type de chaque machine.
Les différentes variations possibles par exemple sur un tour :
Puis il faut faire la simulation d'usinage.
La nouvelle simulation d'usinage a comme but de calculer les cotes nominales. Comme dans la deuxième méthode on utilise des cotes bilimites pour calculer les valeurs nominales des CF.
Mais il y a beaucoup plus, dans la simulation si on tient à disposition les variances des machines on va disposer en temps réel d'une analyse de capabilité. Et ceci pour chaque cote du BE. L'idée est de ne plus calculer d'intervalle de tolérance pour les Cf intermédiaires mais simplement de vérifier la capabilité du processus à produire les pièces. Il n'y a plus aucune référence à des intervalles de tolérance du début à la fin de la chaîne : on récupère un plan client la simulation d'usinage détermine notre capabilité à produire la pièce. Le seul suivi qui reste à faire est une mesure par cartes de contrôle que le processus reste dans les limites qui ont servi au calcul de capabilité. Puisque l'on sait par la simulation que si la variance du procédé est conforme à la variance connue les pièces seront bonnes en sortie.
Toute mesure en interne d'une Cf comme paramètre de décision pour savoir si l'on continue à produire cette pièce est contre productive. Reprenons l'exemple vu plus haut. Si on fait la mesure sur une pièce de la Cf1 on va rejeter une pièce sur cent alors qu'en fait en contrôle final seule une pièce sur 1000 000 aurait été mauvaise. C'est dû au fait que souvent les écarts se compensent. On dit en statistique que les variances s'ajoutent.
Pour surveiller que le processus reste contrôlé on va par contre calculer des limites inférieures et supérieures des cartes de contrôle associées aux cotes de fabrication.
D'autre part l'étude de capabilité associe un écart type à chaque cote BE. On peut donc estimer en utilisant la loi normale le taux de rebuts de la production. Ceci peut être utile pour déterminer un coût de revient.
- Avantages
- cette simulation tient compte des variations dues à la mise en place de la pièce sur le porte pièce.
- simplicité du calcul des CF nominales.
- indication immédiate de la capabilité à réaliser chaque cote BE
- indication immédiate du taux de rebut estimé
- indication immédiate des lignes centrales et limites des cartes de contrôle associées aux CF
- Inconvénients
- calcul un peu plus compliqué que précédemment
- nécessite d'avoir des informations précises sur son outil de travail
Exemple numérique
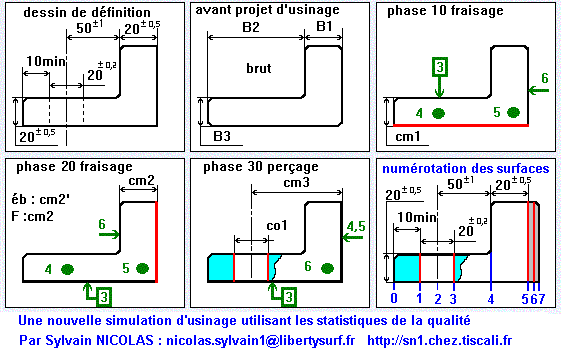
Cliquez pour voir les trois façons de procéder ainsi que leurs effets sur la réalisation en atelier. Cliquez ici pour charger le tableau au format XLS.
Conclusion
Ce simple exemple montre les effets du mode de calcul des cotes de fabrication sur le travail en atelier. On voit que dans les deux premières approches l'ordre de calcul influe sur les tolérances des CF. Ceci montre la limite de ces logiques : une même valeur pour une CF peut déclarer une pièce bonne ou à mettre au rebut suivant le mode de calcul de la cote.
D'autre part même si la deuxième méthode répartit mieux l'IT elle ne nous donne aucune information sur notre capabilité à produire la pièce.
L'intérêt de l'approche statistique est fort. Elle indique a priori notre capabilité à produire toutes les cotes du dessin de définition. Ceci permet rapidement de choisir un autre mode de production ou de dialoguer avec le BE. Elle fournit toutes les limites de contrôle pour le suivi des CF. Elle indique un taux de rebuts prévu pour meilleure estimation. Elle s'intègre donc naturellement dans la démarche qualité d'une entreprise certifiée ISO.
|